Pland Stainless
Multi-Purpose, Bespoke Boxes to Protect & Transport Sluice Sink Units
Pland Stainless established itself as a commercial sink and hospital equipment supplier.
They now manufacture and supply stainless steel washroom and sanitary-ware products. With over a century’s experience, Pland Stainless have an enviable reputation as a highly skilled curator of bespoke solutions for a wide range of sectors.
We’ve been working with them since 2016 and earlier this year, our latest project got underway. The design and creation of protective packaging for a series of sluice sink units, primarily provided to the healthcare sector.
The Protective Packaging Aims
Nicknamed ‘slop-hoppers’, sluice sinks are used to safely dispose of liquid clinical waste. From the contents of a drainage bag to vomit bowls, slop-hoppers are found in places like hospitals, GP surgeries, and nursing homes.
Pland Stainless were after a protective packaging solution for their sluice sinks. The box had a trifecta of aims to meet:
- Reduce or eliminate unnecessary packaging materials
- Improve the efficiency of the packing team at Pland Stainless
- Enhance the safe and secure transportation of the sinks to minimise the risk of damage
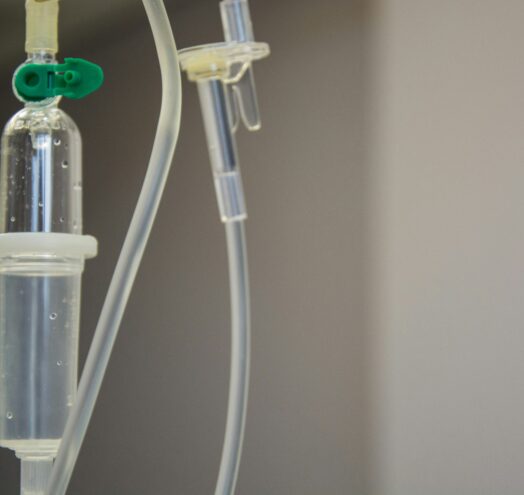
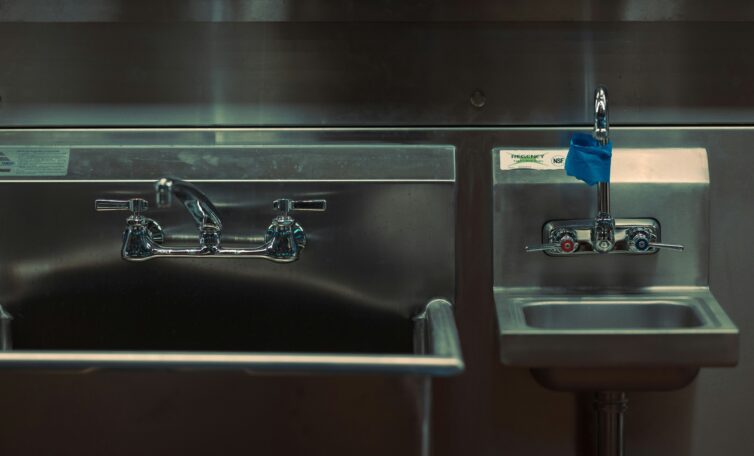
The Project
Having worked with Pland Stainless for around eight years, we’ve come to understand their needs and wants from the packaging solutions we design for them. And they were more than trusting in giving us the freedom to apply our experience of past solutions to this new project!
Each package would house:
- One of three different sized sink units
- A pair of wall-mounting brackets
- Various other fixtures and fittings
Given the size, shape, and heavy weight of the sluice sink – plus these additional items – a bespoke packaging design was a given.
Yet, we needed the solution to ensure Pland Stainless packing team’s could carry out their role as efficiently and time effectively as possible. So, a simple design was in order!
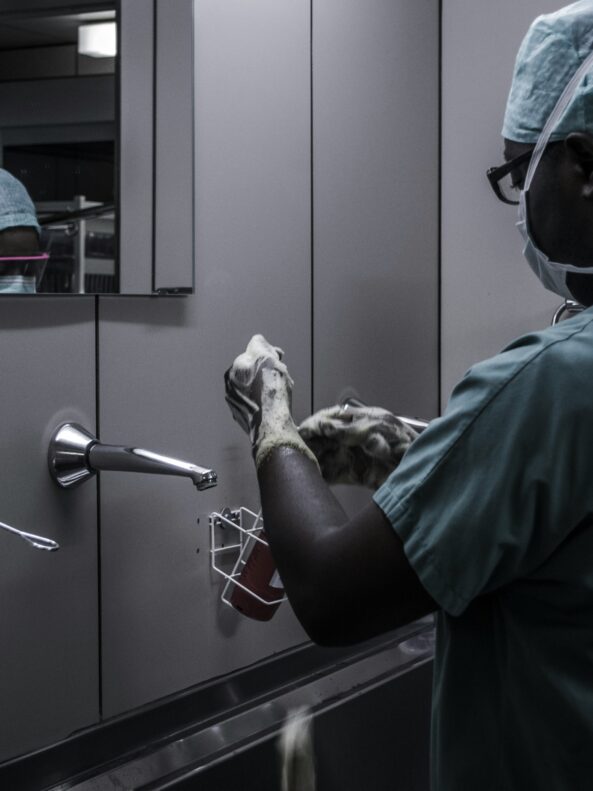
Bespoke Packaging Design
for a Bespoke Product
Traditionally, making up a box and adding its fitments are done separately. The various elements are usually brought together at the end. But the sheer weight of this steel product meant we had to think out-of-the-box when it came to assembling this package!
| Box is flat, and sink sits in the middle of it
| Internal end caps are fixed to the sink
| The box can be made up around the sink unit and sealed in one
There wasn’t a part of this entire solution that wasn’t unique or original! We developed and manufactured this highly bespoke packaging design from scratch to make sure all three of Pland Stainless’s aims were met.
Matthew Kay, Assistant Commercial Manager at Greyhound Box
The Outcome
For the first order in February 2024, we delivered over 300 boxes. These accommodated Pland Stainless’s range of sink unit sizes.
For the first order in February 2024, we delivered over 300 boxes. These accommodated Pland Stainless’s range of sink unit sizes.
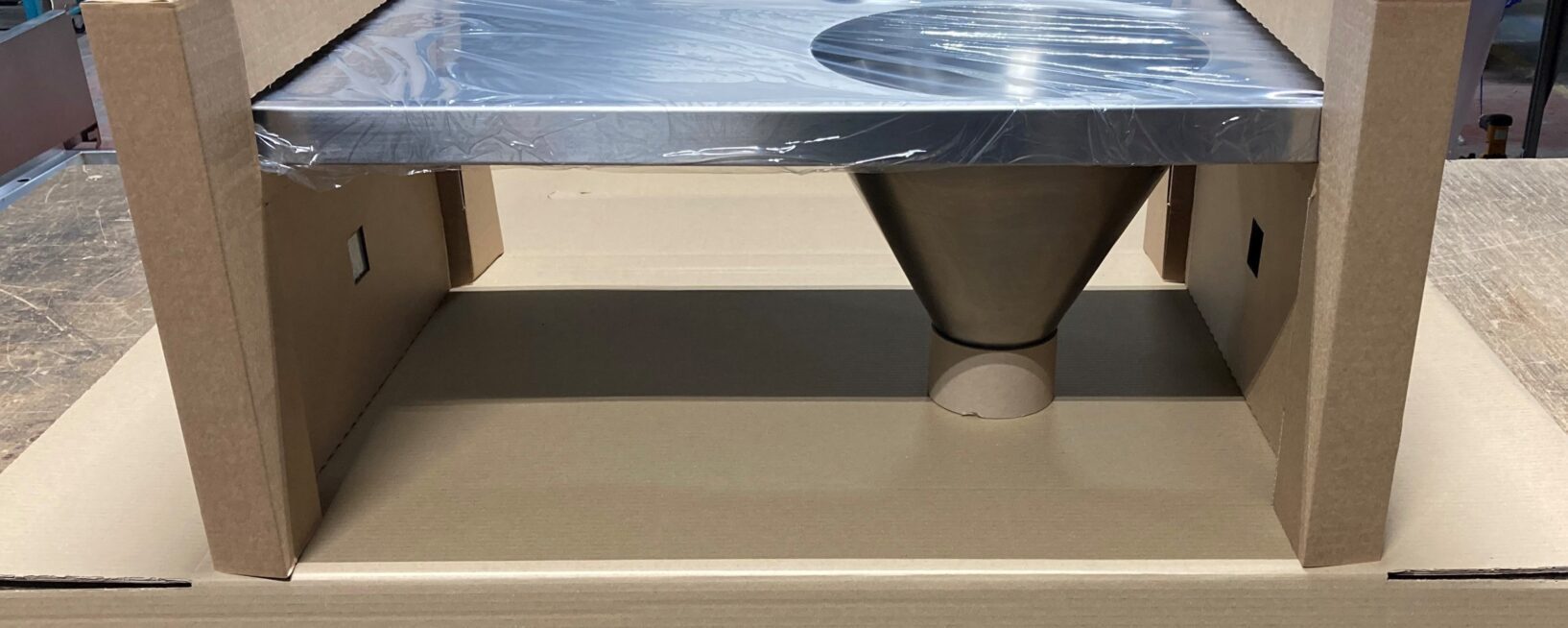
We have worked with the team at Greyhound Box to improve our packaging for our slop hopper sink. Our targets were to reduce the cost of packaging and time it takes to package the product, whilst offering packaging with a higher recycled content – and to secure the item to prevent any damage in transport.
We are thrilled with the final outcome and that each target was looked at in detail.
Ryan Midgley, Buyer at Pland Stainless
What’s Next?
We’ve since taken a second order.
Pland Stainless are very happy with the final packaging design for these sluice sinks, not least thanks to the huge reduction in required packaging materials. One benefit saving both valuable storage space and time to pack!
We know Pland Stainless have been busy reviewing the packaging used for other products within their portfolio, with similar aims to reduce unnecessary extras and improve packing efficiency.
We’re looking forward to getting underway with more solutions that have bespoke and improved design at their core!
Matthew Kay, Assistant Commercial Manager at Greyhound Box
Could your products benefit from a packaging review and redesign?
Get in touch to find out how to get started!