Autocharge
Overcoming Complex Requirements to Package Automotive Products
Driving Innovation
in Automotive Packaging
Autocharge is a supplier of starter motors, alternators, and turbocharges, and provides products for all specialist and general automotive applications including commercial, plant, marine & agricultural.
We’ve had a working relationship with our local friends since 2016, supplying unique packaging solutions that cater to the needs of their specialist products.
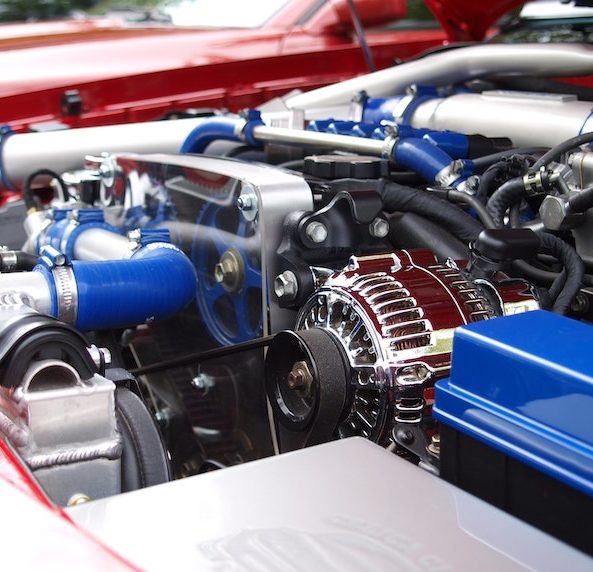
A Bespoke Challenge
Graham Corbett, Product Manager, approached us to provide a bespoke packaging solution for the launch of their new steering rack.
The product came complete with complex shape and weight requirements, including three different sizes.
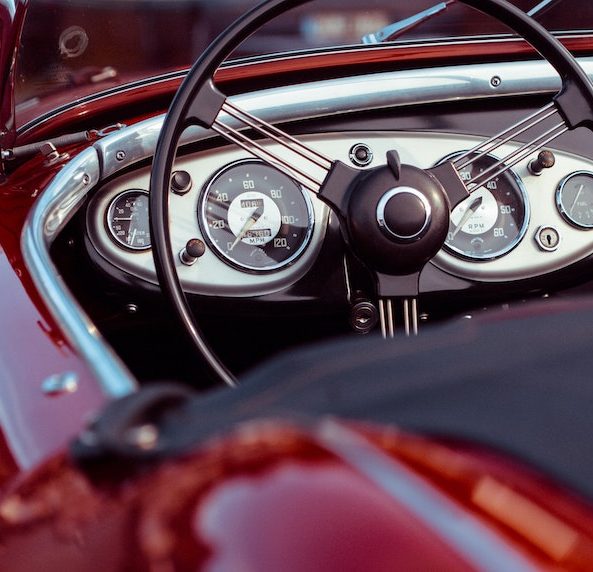
Pedal to the Metal
Just a day after Graham’s enquiry, Louise and Claire visited Autocharge’s HQ to see the product and discuss its specific packaging demands in granular detail.
By getting Graham to fully list the issues Autocharge was up against with packaging this product, we came away with a full understanding of exactly what the packaging solution needed to resolve.
It became a Greyhound Box family affair, with our Design Team heading over to Autocharge’s HQ to provide specialist expertise and develop the solution.
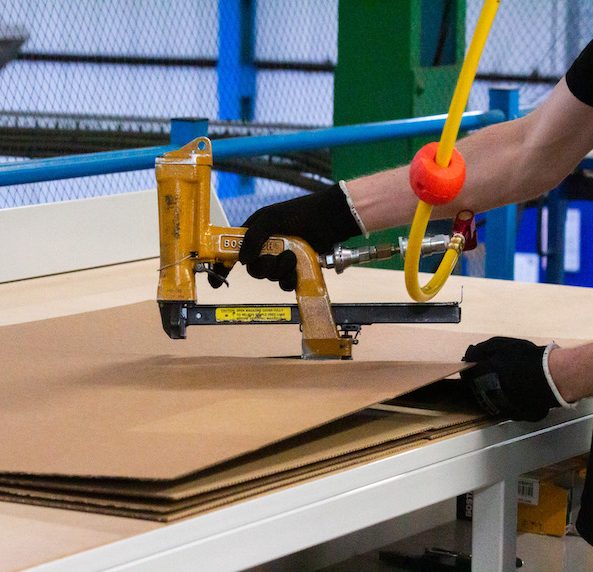
The Design Team’s obvious wealth of knowledge of the processes and technicalities took me through what was possible, the limitations of some of my ideas, and all the solutions to the many issues.
Graham Corbett, Product Manager
The Corrugated Solution
We engineered corrugated cardboard to develop:
- Three outer boxes in different sizes to accommodate the entire product line
- One universal inner fitment to hold the product in place
- Same-style boxes with 2-colour printing of Autocharge’s branding for consistency, familiarity, and ease when packing
- Bespoke fitments designed for use with each of the outer box sizes
- A strong, double-wall grade for the outer boxes
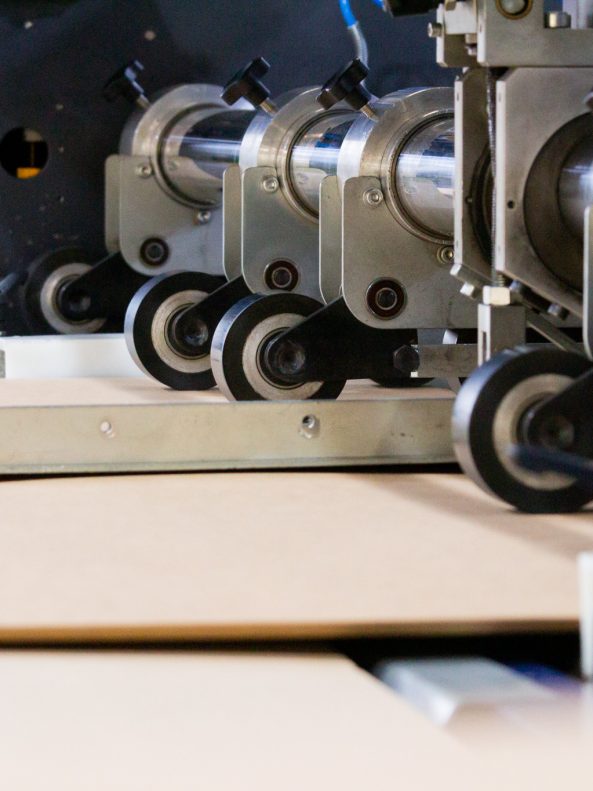
Steering Into Packaging Success
800 units across the range were produced and delivered on the first order.
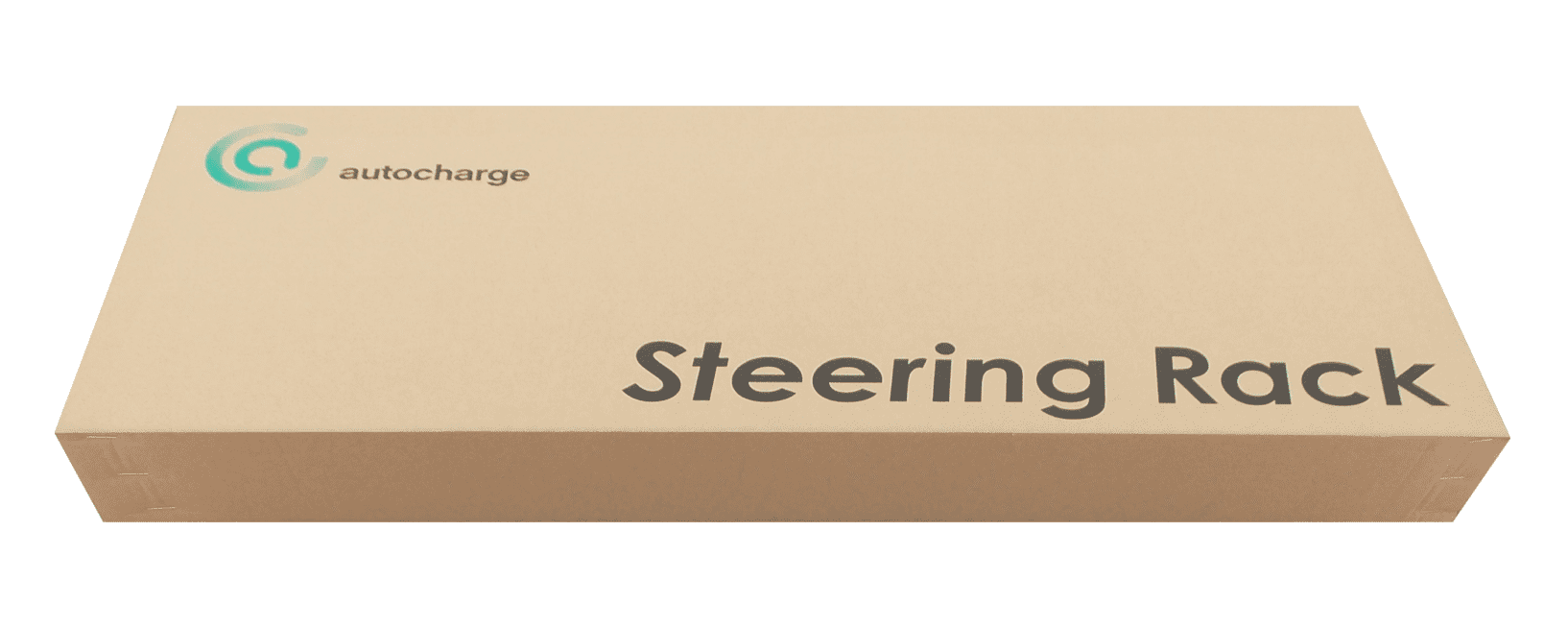
Reinforcing our already-tenacious working relationship, aspects of the design could be tailored in real-time to meet exact requirements, meaning the project was a huge success!
Greyhound Box made what seemed to be a tricky project to bring to fruition a walk in the park, delivered on-time and within the allocated budget.
Claire, Louise and the team were nothing but positive and professional, throughout.
After visiting the Greyhound Box production site, being shown sample products, processes required, and making quite a few tweaks, we were finally ready to have the packaging and artwork approved and signed off.
The process is now all done, and we have a delivery date for the packaging well within our target date.
Graham Corbett, Product Manager